Image processing is fundamental in machine and computer vision. It uses algorithms to manipulate digital images to enhance their quality or extract information, and breaks down an image into pixels, manipulating them to achieve desired effects.
Machine vision uses cameras or videos to analyse images in industrial settings to inform manufacturing processes. Computer vision uses image processing to recognise and categorise image data. For example, autonomous vehicles use computer vision to identify road users, road signs, and obstacles. Some of the key image processing techniques include filtering, edge detection, segmentation, feature extraction, and pattern recognition.
Contrast: The key to reliable image processing
Reliable image processing relies on achieving the highest possible contrast to clearly distinguish between acceptable and defective parts. For this, traditional imaging setups often require multiple components - such as the camera, lighting, lenses, and protective enclosures - to be individually sourced, assembled, and integrated. This complexity can lead to higher costs, time-intensive setups, and frequent maintenance needs for decision-makers, developers and integrators involved with the economic solution of image processing applications in OEM machines.
Michael Steinicke, Product Manager at Baumer Group, explains: “In addition to selecting the camera, the right components must be chosen to solve the application. This also concerns questions of procurement, long-term availability and size. Installation and maintenance are key issues for OEMs. The image processing system often needs to be enclosed, i.e. protected. It must then also fit into the installation space and be accessible at the same time. However, proprietary solutions made from standard parts tend to be rather large.”
These space constraints, combined with what can often be harsh industrial environments can create further obstacles, particularly if strict deadlines are involved. Industrial imaging systems must be robust enough to withstand challenging conditions, while also compact enough to fit seamlessly into tight spaces within machinery or production lines. For many professionals, the process of combining various imaging components - each with its specific maintenance and compatibility requirements - can be costly and time-consuming.
Addressing these pain points requires a shift towards simpler, more cohesive imaging solutions. As more companies seek ways to reduce installation time, lower costs, and enhance operational flexibility, the need for a powerful, all-in-one vision system has become apparent. Continues Steinicke: “It is obvious that a plug-and-play component, which is also small and easy to procure and quick to install, significantly minimises the effort on the customer side and helps with a short time-to-market.”
The need for all-in-one solutions in modern imaging
In response to these challenges, all-in-one imaging systems are emerging as a promising alternative to multi-component setups. These solutions integrate the camera, lighting, lenses, and sometimes additional features such as protective enclosures into a single, streamlined unit. In doing so, all-in-one cameras could help to reduce the complexity of imaging setups and enable faster deployment, easier maintenance, and greater compatibility with existing machines.
Baumer Group recently introduced the IXG All-in-One GigE Vision Camera for just this purpose.
Baumer is reputed as a reliable partner for simplified industrial image processing at improved cost-efficiency and user-friendliness. The IX series coming in all-in-one design is the most recent example.
Built to handle mainstream applications with the efficiency of Smart Vision and the power of PC-based imaging, the IXG helps to simplify machine vision while maintaining industrial-grade performance. Steinicke explains: “The approach has met with great interest and perhaps even more applications can be addressed than one might think at first glance. There is a lot of charm in the possibility of solving image acquisition as simply as with Smart Vision with just one piece of hardware, but on the other hand using a high-performance PC with all degrees of freedom - including software and user interface. Or even to set up a ‘simple’ multi-camera system based on the same principle.”
Introducing the IXG: Baumer’s answer to modern imaging needs
The IXG All-in-One GigE Vision Camera is designed to overcome many of the challenges associated with traditional setups. It offers a compact, high-performance solution that integrates a camera, lighting, and optics within a single, rugged unit. With its small footprint - measuring only 5cm - and IP 67 protection rating, the IXG is engineered to withstand harsh conditions and tight installation spaces, ideal for demanding industrial environments.
The camera’s all-in-one design provides a number of advantages. It delivers a pre-integrated solution that fits easily into existing systems and workflows, saving on both installation and maintenance time. Another advantage lies in the IXG’s flexibility in software and data control. The camera is fully compatible with PC-based vision systems via its GigE Vision interface, allowing users to tap into the processing power of a PC while retaining the simplicity of a self-contained device. This is particularly valuable for industries that require data logging, real-time access control, and detailed customisation - common in pharmaceuticals and packaging, where traceability is critical.
High-performance and compact design
Despite its compact size, the IXG camera is designed for high performance. Steinicke reveals: “The IXG is designed to work with high performance at up to 50 fps, which is also supported by the lighting. The illumination is suitable for many applications in the specified image field, but is restricted by the camera size, which sets limits. Such limits can occur if a polarising filter is used to prevent reflections at minimum exposure time, which typically absorbs 75% of the light. In principle, the IXG can also control external lighting - analogous to conventional approaches - but this is somewhat contrary to the idea of “all-in-one”. Otherwise, we see no limitations - the lenses, autofocus and image sensor correspond to industry standards.”
The lens options offered with the IXG - 6mm, 8mm, and 16mm - are optimised for typical industrial working distances and field sizes. Baumer carefully selected these focal lengths to address the most common application requirements, including quality control, identification, and object positioning tasks. Steinicke explains: “Many applications are solved with short working distances and that certain image field sizes are already predetermined by the objects to be examined. This can be addressed with the current focal lengths. At the same time, the integrated lighting must support these image fields. But of course, such a small product makes little sense for working distances greater than 1m. Below that, these three focal lengths allow you to work flexibly with distance and field of view.”
Applications across diverse industries
The versatility of the IXG camera makes it suitable for a range of applications. In pharmaceutical and packaging sectors, it can serve as a reliable multi-camera system for identification and quality control, ensuring compliance with stringent industry standards. It also supports additional tasks, such as object positioning and presence verification, where high precision and reliability are required.
Beyond these immediate applications, the IXG is poised to support emerging needs as more industries adopt automated vision solutions. The camera’s ability to integrate into multi-camera setups or function as a standalone unit could make it a strong candidate for track-and-trace systems, quality inspections, and other complex, high-speed imaging tasks.
Long-term ROI and the benefits of an integrated system
For industrial users, the IXG’s compact, integrated structure reduces the need for additional enclosures and components, simplifying the supply chain and lowering upfront costs. Moreover, its ease of installation and high durability mean that companies can expect reduced maintenance requirements and faster installation times, minimising costly downtime. Concludes Steinicke: “Another aspect is the possibility of retrofitting existing machines thanks to their small size and GigE compatibility - e.g. for track and trace. This means that the service life of existing machines can even be extended.”
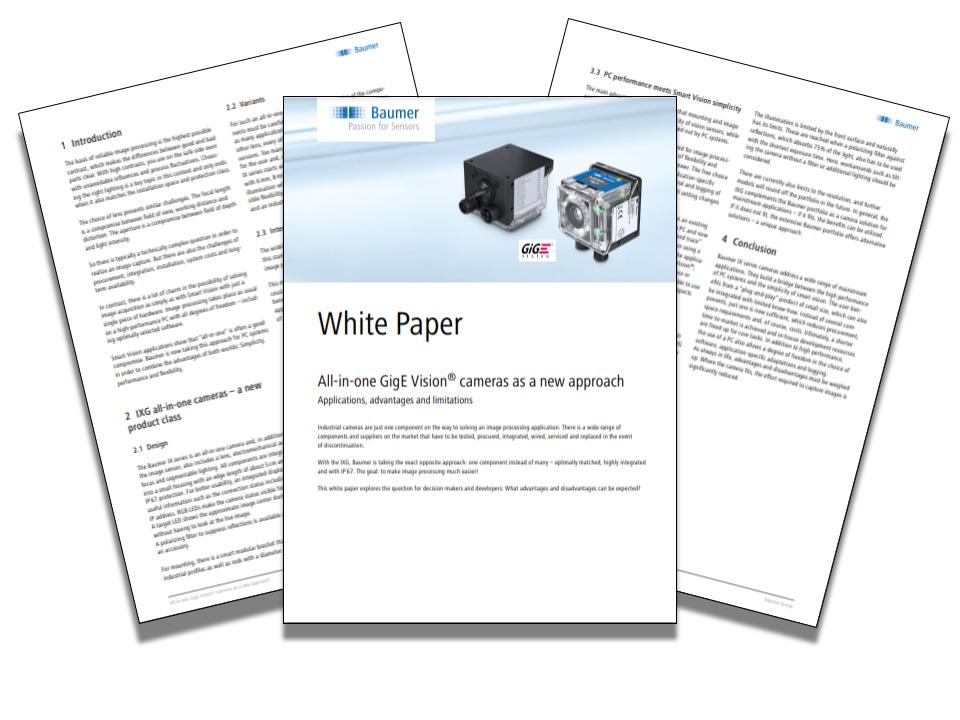