ISTECH provides turnkey custom automation solutions for a variety of industries using advanced computer and automation technologies
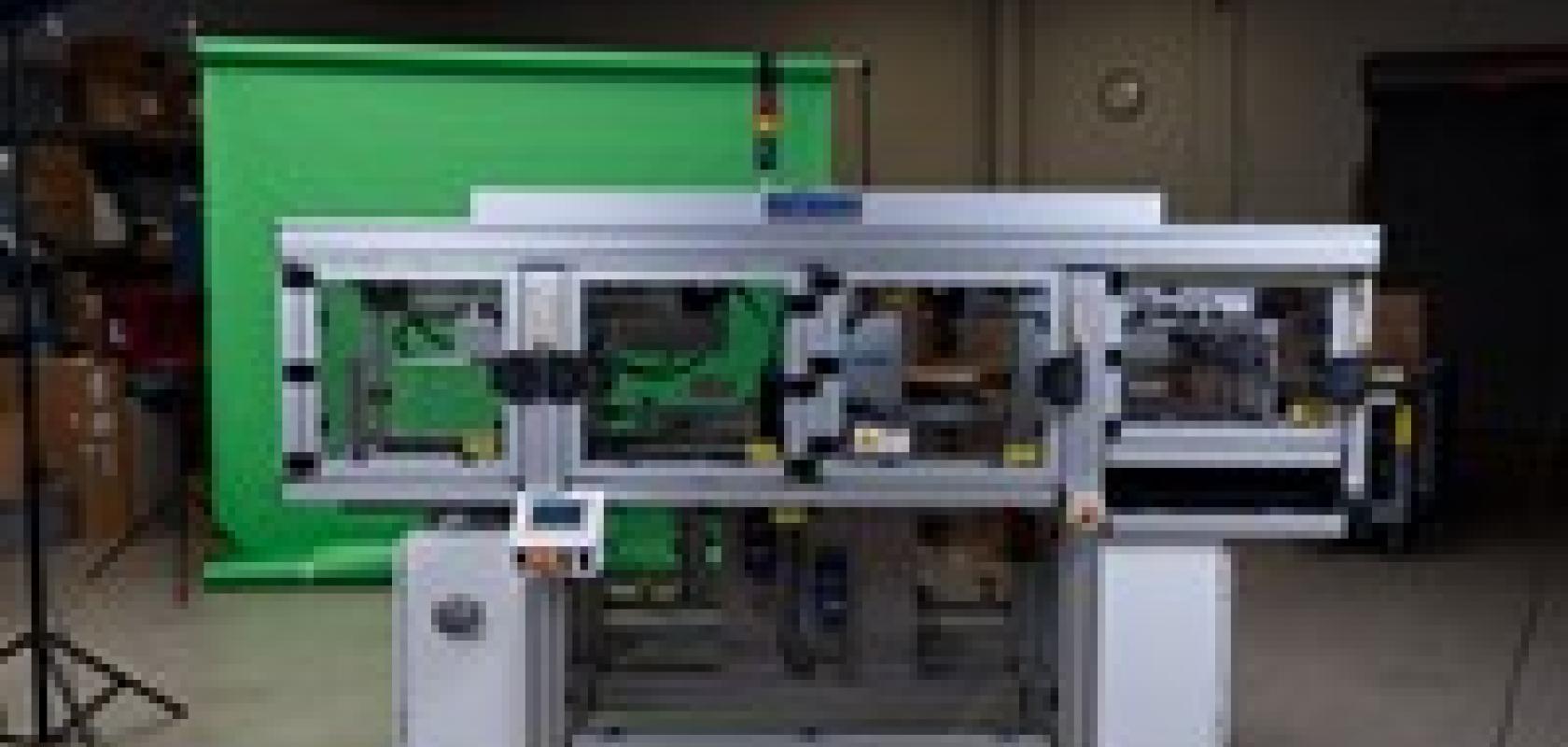
If you haven’t incorporated machine vision on your automation line or machines recently, you could be missing out on some powerful and cost-effective solutions that you probably didn’t know were out there. Take it from Andy Wright, Manager of Automation Engineering at ISTECH (Dover, PA), which provides turnkey custom automation solutions for a variety of industries using advanced computer and automation technologies.
“We’ve been integrating vision for quite awhile at ISTECH,” Wright said. “Our distributor, Faber Industrial Technologies, had been encouraging us to try Teledyne DALSA’s vision systems for some time—and, based on how happy we were with the cost and performance of our first project, we’ll definitely use Teledyne DALSA products in the future.”
Perfectly aligned
ISTECH’s first project using Teledyne DALSA vision consisted of designing and building a custom assembly machine for Conductive Technologies, a long-time customer in the medical device industry. The machine applies lids—clear plastic strips that come on a roll and peel off like labels—to sheets of plastic substrates. Each sheet has six silk-screened substrates, or coupons, on it. In order to apply the lids reliably and accurately to meet production goals, a series of features on each lid must be aligned with each corresponding coupon.
Plant floor personnel had been performing this process by hand; however, this method lacked consistency, was time consuming, and did not provide the required throughput and accuracy. As a result, ISTECH engineers designed a machine vision system into the assembly machine.
Four high-resolution, GigE cameras are connected to a Teledyne DALSA GEVA industrial controller. GEVA provides expandable Gigabit Ethernet camera interfaces that significantly decrease system costs for multi-camera applications like this one. Two of the cameras are positioned on opposite sides of the sheet, while the other two are located at each end of the lid.
After a sheet is loaded onto a moving vacuum table, the sheet cameras identify and locate the six coupons. The lid cameras identify and locate the corresponding features on each lid. Teledyne DALSA’s Sherlock vision system software then performs calculations and provides X, Y, and rotational correction values. These values are transferred to an Epson robot, which positions the lid on each coupon accordingly. Heat sealers then attach each lid. Once all six coupons are complete, the sheet is offloaded to a stack for further processing.
Getting in—or out—of sync
The Teledyne DALSA machine vision system’s ability to process information asynchronously was essential to the success of this application. In order to achieve the required cycle rates, ISTECH programmed the robot to work ahead, so that, while one sheet is being taken off the vacuum table, a new lid is ready to go as the next sheet is loaded.
Normally, the vision values are completed first for a given coupon; however, during the sheet exchange sequence, the lid data is calculated first. As a result, information from the cameras must be transmitted asynchronously.
“Using the Sherlock software, the Teledyne DALSA system handles asynchronous communications quite well,” Wright says. “The algorithms in this application were straightforward—the data handling is what made the Teledyne DALSA machine vision system so successful in this case.”
A pleasing performance
When the machine was first installed, ISTECH’s customer, Conductive Technologies, stringently evaluated the product that came off the acceptance run. Both accuracy and throughput were deemed excellent. Before the system was installed, human assemblers at Conductive Technologies required several minutes to align and apply lids to each sheet.
“Our spec was to run one sheet in 30 seconds, and we were able to beat that rate,” Wright says. And, since the machine has been installed, Conductive Technologies reports that lid placement accuracy far exceeds the project’s initial goals.
“I am particularly impressed with the Sherlock software since it provides an extremely powerful set of programming tools in a cost-effective product,” Wright says. “I look forward to integrating Sherlock in future projects.”
After each plastic substrate sheet is loaded onto a moving vacuum table, Two GigE cameras identify and locate the six coupons.
Two additional GigE cameras identify and locate the corresponding features on each lid. Sherlock vision software performs calculations and provides X, Y, and rotational correction values, which an Epson robot uses to position the lid on each coupon accordingly.