Sourcing the Best Camera for Your Vision System
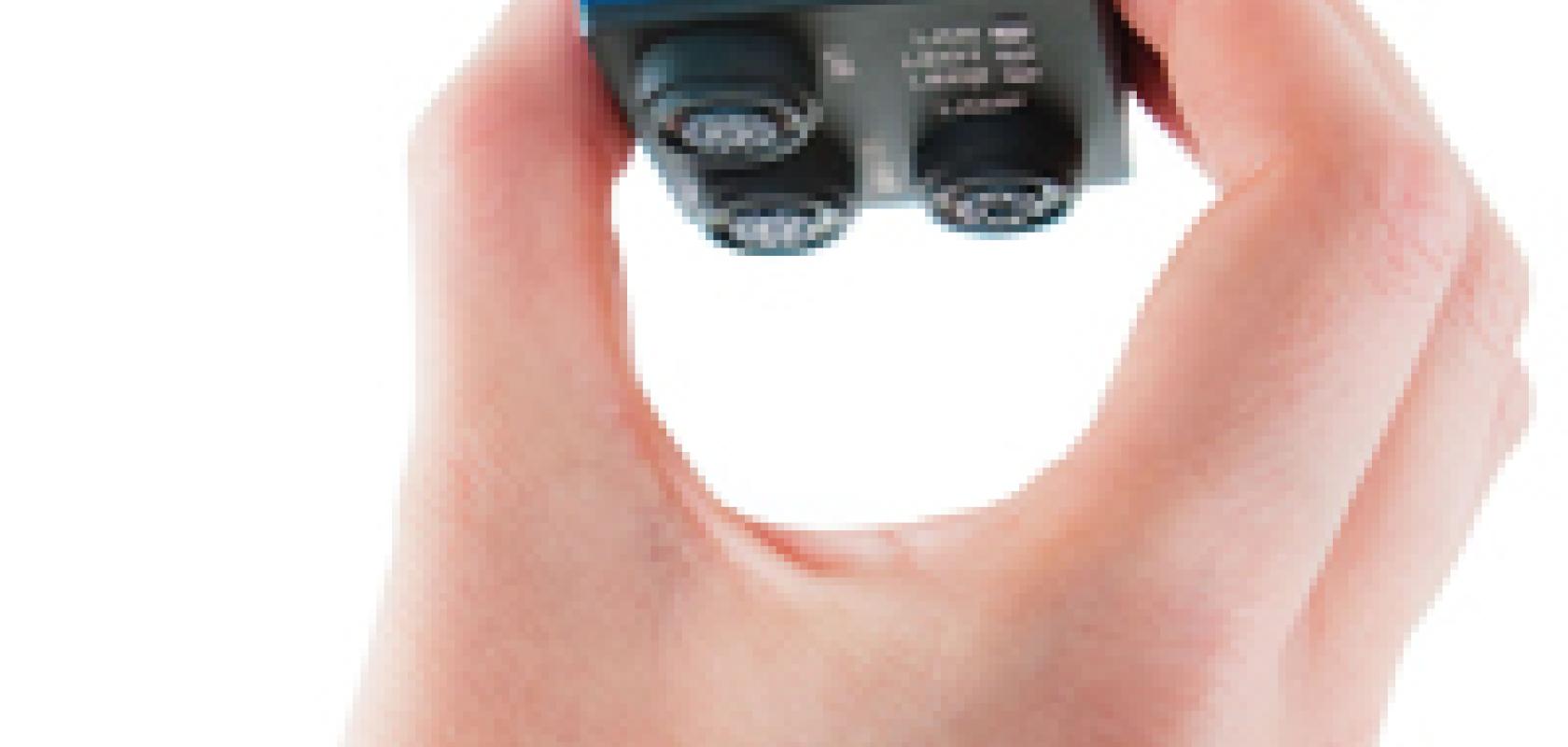
The easiest way would be complete transparency – show a camera manufacturer your application and ask them what you need. Unfortunately, you can’t always do that. There are usually confidentiality requirements and proprietary technology that you can’t disclose. So if you can’t disclose everything, what do you need to tell a camera provider so they can help you get the best possible camera for your application?
Camera Type
In machine vision there are two primary types of cameras: line scan and area cameras. While other types of cameras and sensors exist, like time-of-flight sensors, most machine vision applications are addressed with cameras that fall into these two broad categories.
There are always exceptions to any rule, but one good rule to determine which camera type is by asking the following question: “Will the camera be looking at a discrete component or a continuous ‘web’?” If it is a discrete component, an area camera may be a good choice. If it is a continuous web process, such as paper, aluminum, steel, glass, or fabric, a line scan camera may be the right camera for the application. One exception to this rule is if the discrete component you are looking at has very high-resolution requirements in one or both dimensions. Line scan cameras offer higher resolution than area cameras in one dimension. And by scanning the object at a greater number of lines over the length of the object, you can achieve even higher resolution in the second dimension.
Resolution
In order to choose the right camera for the job it is critical to know the resolution requirement (i.e. the number of pixels covering the field of view). Calculating the resolution requires knowing the size of the field of view and knowing the smallest object you wish to resolve. Since I stipulated that we will not cover optics in this discussion, we will assume that the optical magnification is 1. In other words, no magnification. This means that the field of view can be directly related to the number of pixels on the camera. For example, if the field of view you want to image is 4” x 2” and you need 1,000 pixels per inch, you know you need a camera which has a minimum resolution of 4,000 x 2,000 pixels.
How do you decide how many pixels you need? Let’s look at a basic machine vision operation: defect detection. To find defects as small as 1/100” x 1/100”, most machine vision experts will tell you that it is prudent to have more than one pixel cover a defect in order for reliable detection. A rule of thumb that many vision experts use is to have 3 pixels in the smallest area you want to detect. This means, in our example, you want roughly one pixel for every 3/1,000” of area you are covering. If we are imaging a 4” x 2” field of view, and we need a pixel every 3/1,000”, this means we need 1,200 pixels (4” / 3/1,000”) x 600 pixels (2” / 3/1,000”) at a minimum.
Acquisition Rate
How fast does your camera need to go? For area cameras and discrete component inspection, this is a very straightforward question. What is the rate at which your “widgets” are going by a single point in space? If the answer is 25 widgets per second, then you need an area camera whose minimum frame rate is at least 25 frames per second (fps). It is always a good idea to leave some tolerance padding on all of these specifications, so let’s say that a camera with a minimum frame rate of 30 frames per second is a good choice.
There is a second dimension to this question that involves exposure time. Not only does the camera’s frame rate need to keep up with the widget rate, but the host computer also needs time to perform image processing and make whatever decisions it needs to make (e.g. reject part). This is part of the overall “cycle time.” If the camera is being triggered at a rate of 25 fps, in the time domain that is 40 milliseconds (ms) per frame. 40 ms is then your cycle time. All the image acquisition, transfer, and processing must take place within that 40 ms window. If we know it takes the host computer 20 ms to process each image, and we know it takes 5 ms to transfer the image from the camera to the host computer, then we know there is only 15 ms left for exposure time. Some of these processes, like exposure, are serial processes, but others can be overlapped. The timeline in Fig. 1 below details this:
Notice in the above timeline that processing can begin on the first frame as soon as it is received, and the second frame exposure and transfer can happen in parallel with the first frame transfer and processing. However, processing cannot begin on the second frame until the processing is completed on the first frame (unless you employ multi-threaded processing with multiple core processors).
For line scan cameras, speeds are specified in lines per second rather than frames per second. To calculate the minimum speed required of the line scan camera, we need to know two things: 1) resolution (which we discussed in the previous section) in the direction of motion; and 2) the speed of the object being imaged. If we need a pixel resolution of 3/1,000” and our object is moving at 100” per second, we will require a line-scan camera speed of 33,333 lines per second, or 33.3 kHz line rate (100” / 0.003” = 33,333).
Interconnect
There are multiple interconnect standards [insert your joke here] that connect cameras to host computers. Some require framegrabbers, such as RS-170, NTSC/PAL, CoaXpress, Camera Link, and Camera Link High-Speed (CLHS). Others rely on interfaces that are typically built into computers and are ubiquitous, such as Gigabit Ethernet (GigE), Firewire (IEEE1394), and USB variants. For camera manufacturers to choose the right interconnect, we need to know bandwidth requirement (which is a product of resolution and frame rate) and distance between the camera and host computer. Since analog-based interfaces are going away in favor of digital interconnections, we can say that GigE offers the greatest transmission distance, while CLHS offers the highest throughput.
Light Wavelength
Cameras vary in their sensitivity based on wavelength of light. Knowing if a particular wavelength of light is going to be used to illuminate the object in question is of critical importance to the camera manufacturer. With laser illumination, it is easy to find the light wavelength – that will be part of the laser’s specification. It is a bit more difficult to know the wavelength distribution of a halogen light (more toward the red end of the spectrum) or a fluorescent light (more towards the blue end of the spectrum). You can generally get the component wavelengths from the lighting manufacturer.
Quantity
Sometimes an application will require a bit of functionality that is just outside those of a standard product. It may be possible to perform a modification to the camera to make it perfect for a given application. Camera manufacturers who manufacture a high volume of cameras may want to know what the volume potential is for a modified camera. If the application is a “one-of-a-kind” and only requires one camera, this may limit a manufacturer’s ability to produce a custom modification. On the other hand, an application that, if successful, will require a high volume of cameras on an ongoing annual basis, may be a different story.
Price
This requirement would have been listed first if these items were ranked by importance. Obviously price is a very important part of any purchasing decision – including vision systems. It is not the only concern, however, since a vision system that cannot do the job is not worth anything to the customer. Again, it goes without saying that you want to find a camera and vision system that will do the job at a reasonable price for the application. The reason price enters into the discussion of “Things We Need To Know…” is because some of the above items are nuanced. For example, on the question of acquisition rate, I have often heard customers request a camera run “as fast as possible,” when what they really mean is “as fast as possible within my budget.” Knowing the target price range can help to narrow the camera selection to those that will work from both a performance standpoint and a cost feasibility standpoint.
It’s important to be straightforward with your camera provider about your price range. The best providers are more interested in you being a satisfied (and hopefully returning!) customer than making an extra 20% by selling you more than you need. The more information you can provide, the happier you will be with your new camera and the price you paid for it.
And if you don’t have a price range…well that requires another article about a much more difficult conversation.